LS Central 26.0: Fashion, replenishment, and aggregated inventory
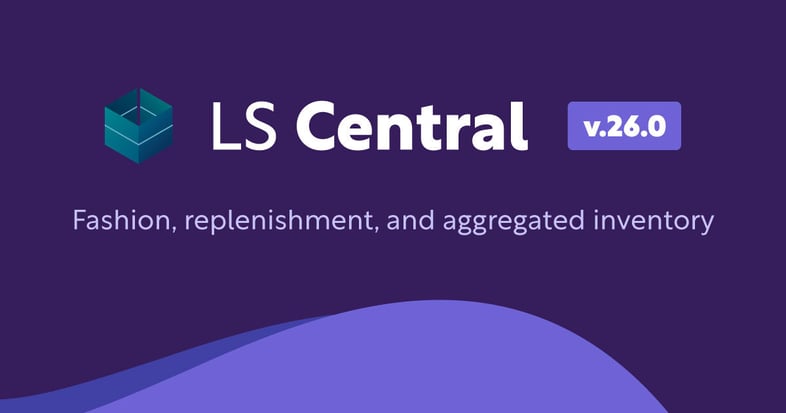
LS Central version 26.0 was released on April 10th 2025. Here’s an overview of what we have added and improved for fashion and replenishment.
Fashion: Improved variants handling in order documents
We have improved how variants are handled in various order documents and made the variant dimension matrix available to more document types for a more streamlined experience when working with item variants in the order documents.
Simpler and faster maintenance of variant document lines with the improved variant dimension matrix
We have improved and streamlined the variant dimension matrix across all document types, to offer you a more consistent experience when working with item variants in various order documents. In the dimension matrix, the quantity of the variants is now shown by default in the base unit of measure. The document lines for the variants are also created in base unit of measure, but you have the option to change it to the unit of measure that is selected in the item document line.
You can also directly enter a quantity on the document line for the item, and the quantity will be distributed among the variants either according to their variant weights, the collection framework pattern, or proportionally based on the existing quantity in the variant document lines.
Easier access to variant document lines
You can now view the document lines that are created for the variants, which was previously impossible, by using the Show Lines functionality that we have introduced in the order documents. You can even update the quantity or delete the document lines for the variants from the relevant page.
Variant dimension matrix now available for more document types
Working with an extensive range of order documents? We’ve got you covered. The variant dimension matrix is now available for the following order document types:
- Retail Purchase Order
- Retail Purchase Order Archive
- Retail Posted Purchase Receipt
- Retail Posted Purchase Invoice
- Retail Purchase Return Order
- Retail Purchase Return Order Archive
- Retail Posted Return Shipment
- Retail Posted Purchase Credit Memo
- Retail Purchase Quote
- Retail Purchase Quote Archive
- Retail Purchase Credit Memo
- Retail Sales Order
- Retail Sales Order Archive
- Retail Posted Sales Shipment
- Retail Posted Sales Invoice
- Retail Sales Return Order
- Retail Sales Return Order Archive
- Retail Posted Return Receipt
- Retail Posted Sales Credit Memo
- Retail Sales Quote
- Retail Sales Quote Archive
- Retail Sales Credit Memo
- Retail Transfer Order
- Retail Posted Transfer Shipment
- Retail Posted Transfer Receipt
- Retail Transfer To Be Picked
- Retail Transfer To Be Received
- Retail Planned Transfer
- Retail Transfer Request
- Retail Sent Transfer Request
A more descriptive and meaningful variant dimension matrix
You can now let the variant dimension matrix show the description of the dimensions instead of the values. This makes the matrix more meaningful and better describes the variants that it holds, such as their colors and sizes.
Fashion: New variant breakdown with dimension pattern
We are offering a new approach to break down the reorder point and maximum inventory from the item to the item store records, on top of the existing variant weight approach. When updating the reorder point and maximum inventory for an item with variants, it is now possible to break down the values by dimension pattern and update the corresponding fields in the item store records. This enables you to distribute the values across the variants according to their sales trend in each location, which may vary due to environmental and geographical factors.
Replenishment: Focusing on the right items in the scheduler replenishment item quantity calculation
Speed up the replenishment item quantity (RIQ) calculation by focusing on the right items at the right time. We have introduced the Replenishment Item Quantity Templates, which lets you calculate the RIQ records for a filtered set of items and locations using the scheduler job. You can specify your own item and location filters in the RIQ Template, or you can link the RIQ Template with a Replenishment Template, and the calculation will be done based on the filters specified in the Replenishment Template.
You can calculate the RIQ records for different items and locations on different days by setting up multiple RIQ Templates with different filters, and specifying when and how frequent each of them will be calculated.
Replenishment: A new parallel replenishment calculation approach using job queues
We have introduced a new parallel replenishment calculation approach using job queues, alongside the existing NAS service tiers and background sessions approaches. With the job queues, you can set up more than 10 parallel jobs to split the workload and speed up the calculation. We offer two methods to start up parallel job queue entries, either using the job queue listeners or web service via Entra application users.
The job queue approach supports the calculation of out-of-stock, replenishment item quantity and replenishment journal, and can be used in both LS Central on-premises and SaaS environments.
In our test lab, we have successfully spun up and ran 50 parallel job queue entries, but it is possible to spin up more job queue entries, if needed.
Replenishment: Item balancing improvements in parallel replenishment calculation
When running the replenishment item quantity and out-of-stock calculation in parallel, we have introduced new options for you to manage how the master job will split the item range among the parallel linked jobs.
A more balanced workload by considering variants when splitting the item range
You can now let the master job consider the variants when splitting the item range among the parallel linked jobs. This is especially beneficial when the number of variants varies between your items, as this option allows you to achieve a more balanced workload between the linked jobs.
Defining your own item range for the parallel linked jobs
Do you want to define your own item range for the parallel linked jobs instead of letting the system calculate it for you? This is now possible. All you need to do is enable the Disable Balancing setting that we have added to the Replen. Parallel Jobs page, and the master job will stop calculating the item distribution range. You can manually adjust the job filter string of the linked jobs as needed.
Replenishment: Considering store closed days in replenishment calculation
We have enhanced the replenishment item quantity and replenishment journal calculations so that they will consider the store closed days to facilitate an even more accurate order quantity proposal based on sales demand.
Considering store closed days in average daily sales calculation
You can let the system consider the store closed days when calculating the average daily sales in the replenishment item quantity. By enabling this option, the system will check if the store is closed on any day within the historical sales period according to the retail calendar or base calendar. The closed days and the sales that occurred on those days will be excluded from the average daily sales calculation, since considering those days would result in an average sales quantity that is too small.
Excluding store closed days from stock coverage
You now have the option to deduct the store closed days from the stock coverage period when calculating the replenishment journal with the Store Stock Cover Reqd (Days) or Wareh Stock Cover Reqd (Days) field. The system will check if the store is closed on any day within the coverage and lead time period according to the retail calendar or base calendar and exclude the closed days from the total coverage. This ensures the right number of stock is ordered to support the sales demand of the stores.
Replenishment: Option to include sales from out-of-stock days in average usage
It is now possible to include the sales that occurred on an out-of-stock day in the average daily sales calculation in the replenishment item quantity. This allows you to capture the sales of those items having limited on hand inventory and subsequently replenish them based on their sales demand.
Replenishment: Locking values in retail sales budget
Maintaining the retail sales budget is much simpler and faster, as you can now lock the value of a budget entry into the retail sales budget. Locking a budget entry allows its value to remain unchanged and excluded from the amount distribution when a total value is updated in the budget.
Aggregated Inventory for LS Central
In LS Central 24.0, we introduced Aggregated Inventory for LS Central, intended to speed up posting processes for businesses that experience a high number of inventory transactions across stores. We are constantly striving to improve and add new functionality, so here’s what we’ve added in the latest version.
Support for the Assembly Orders functionality
You can now manage Assembly Orders within Aggregated Inventory. This feature lets you connect sales demand with assembly supply using internal orders.
Here’s how it works:
- The assembly order header reflects what's being produced.
- The order lines show what's being used in the process.
Once Aggregated Inventory is enabled, you'll see both the store location and the aggregated location on the document page. After posting an order, inventory updates to the aggregated location, while entries still track stock at each individual store.
Features like copy document, undo posted document, blanket orders, and quotes are all supported, too.
Support for the manual replenishment functionality
You can now access manual replenishment functionality in Aggregated Inventory. Manual replenishment is a set of tools enabling buyers to purchase and distribute items actively. Manual Replenishment consists of the following functions:
- Buyer's Push
- Stock Recall
- Allocation Plan Distribute
- Allocation Plan Defined
- Cross Docking
Aggregated Inventory includes the information from the Aggregated Inventory Entries when calculating inventory, historical sales, quantities on orders, out-of-stock, and more.
Support for the Store Stock Redistribution functionality
Store Stock Redistribution calculates the quantity needed in the stores and warehouses. It will also suggest what items need to be transferred from other stores and warehouses to meet demand. Store Stock Redistribution provides the following Calculation Types to calculate the supply and demand at the locations:
- Sales Demand
- Stock Balancing
- Reorder Point/Max. Inventory
- Manual Redistribution
- Warehouse to Warehouse
Aggregated Inventory includes the information from the Aggregated Inventory Entries when calculating inventory, historical sales, quantities on orders, out-of-stock, and more.
Support for Stock Coverage and Store
Aggregated Inventory now supports Stock Coverage and Store. Stock Coverage shows how long a store can keep selling certain items based on past sales and current inventory levels. It's especially useful for seasonal or one-time items with a limited shelf life. Store Capacity Management helps control how much space products take up on shelves or in store sections. You can group items by category or season, making sure items are the right size to maintain cost effectiveness while meeting business requirements.
For more information about Fashion, Replenishment, and Aggregated Inventory, visit the LS Central Help.