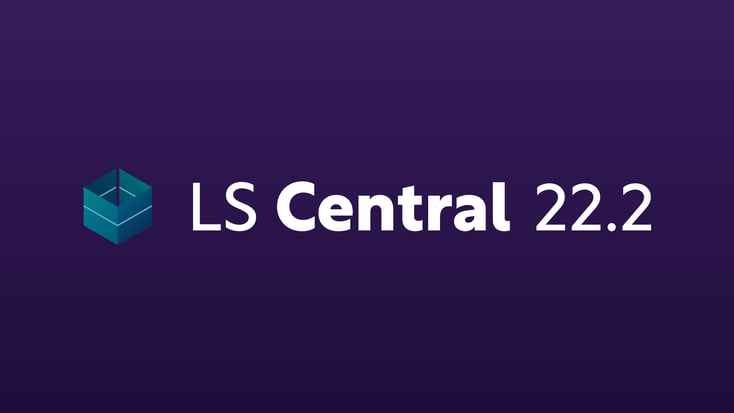
LS Central version 22.2 was released on June 30th, 2023. Here’s an overview of what we have added and improved in the system.
Replenishment: new functionality for BOM and components
We have introduced a new functionality in automatic replenishment to work with the Replenishment Calculation of Bill of Materials (BOM). The solution calculates the demand for BOM items and then breaks down the demand into their components, which are purchased and transferred.
This process is common in hospitality, but is not limited to that industry, as it can be applied to all item types that use the Assembly BOM concept.
New replenishment journals available to calculate components based on demand of BOM
Two new types of replenishment journals have been introduced: the BOM Replenishment Journal and Component Replenishment Journal, to work with the replenishment calculation for the Bill of Materials. The calculation is done in two-steps, where the demand of the BOM items is first calculated in the BOM Replenishment Journal, and then the replenishment amount for the components needed to meet demand for the BOM is calculated in the Component Replenishment Journal. These processes will provide you with the right number of components needed to produce the BOM and serve customer demand.
Now possible to create assembly orders in replenishment
The BOM and components replenishment process supports Make-to-Order and Make-to-Stock BOM items. For Make-to-Stock BOM items, which are produced in advance and stored in inventory, you can create assembly orders in the BOM Replenishment Journal for the BOM items to be produced at the warehouse or stores.
You also have the option to include the quantities from the open assembly orders in the replenishment calculation.
Easier to replenish ingredients in the weekly menu planner
If you use the weekly menu planner to plan for meals in advance, you can now link a Replenishment Planned Event to easily calculate and replenish the ingredients needed. When you connect the Replenishment Planned Event to the weekly menu planner, you transform the meals that have been entered upfront into Planned Sales Demands. The additional sales from the Planned Sales Demands will add to the demand from regular store sales, and the summarized demand will be calculated in the BOM Replenishment Journal.
New option to replenish components without recipes
What if the components are used to produce meals that don’t have a recipe? This scenario is common in fine dining restaurants where meals are prepared without following a strict recipe. Now you have the option to include the negative adjustment and assembly consumption entries for items in the daily sales calculation. This allows the consumption history of the components, which are usually posted as negative adjustments, to instead be tracked similar to the sales history of generic items. The components can be replenished with the average usage method, which uses the standard Purchase and Transfer Replenishment Journals, a similar process used for non-BOM items.